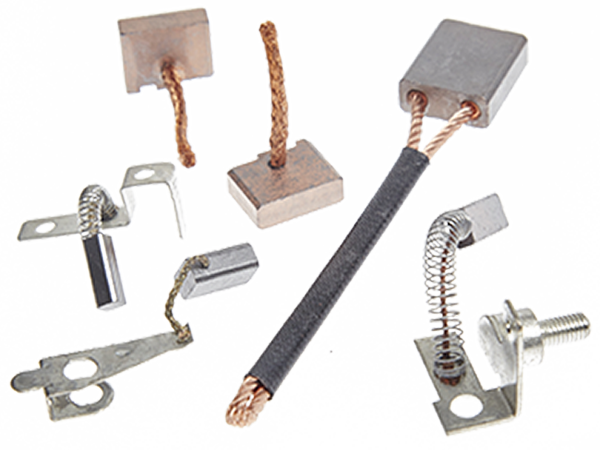
A carbon brush, also known as a motor brush, is the small part of the motor that conducts electrical current between the stationary wires (stator) and the rotating wires (rotor) of a motor or generator. The brush is typically made up of one or more carbon blocks and can come with one or more shunts or terminals.
A motor generally contains more than one carbon brush to conduct electrical current. The brushes are categorized into five brush-grade families, each of which is suited for different kinds of motors and applications.
A carbon brush has three operating parameters: mechanical, electrical, and physical/chemical.
Mechanical
A slip ring or commutator is attached to the rotating shaft. A spring is used to push the brush into the slip ring or commutator to maintain contact. The surface of the slip ring or commutator should not be too smooth/glossy or too rough in order to ensure good brush contact and performance.
Electrical
Electrical Carbon Brush Operator
Electrical current is transmitted from the rotating shaft via contact with the carbon brush. Very small areas of the brush, called contact spots, contact the surface of the slip ring or commutator. The contact spots should be evenly distributed on the surface of the brush to maintain brush balance and avoid damage to the commutator/slip ring surface.
Carbon brushes with high resistivity work best, because this helps prevents arcing at the interface between the brush and commutator/slip ring. It is also important to maintain a proper power density for DC motors to operate at peak performance which often requires removing brushes. Calculations for power density should be performed and brush density optimized if your application changes. Brushes should not be assumed to be missing if you find a DC motor operating with brushes removed.